Plastic coating is the process of dipping or immersing an object in liquid polymers or plastic to apply it to its surface. A finished product is dipped into a liquid polymer and completely (or partially) covered in plastisol. The result is a thick plastic finish for aesthetic and protective purposes, increasing the material’s resilience to abrasions, wear, corrosion, and the elements. Read More…
No one has more dip molding expertise than we do! We were a pioneer in dip molding 60 years ago, and we remain an industry leader today. Reach out for a fast, competitive quote on custom dip molding & coating services, from prototypes to low or high volume. We’re your single source for design consult, quick prototyping, custom formulations & secondary operations.

Precision Dip Coating provides dip coating services for the manufacture of soft plastic parts such as cap plugs. hand grips, and more. Decorative and protective, our services are very cost effective and we have a proven track record for on time delivery and precise manufacturing. We can match any color you need, and offer services such as assembly, die cutting, packaging, and decorating.
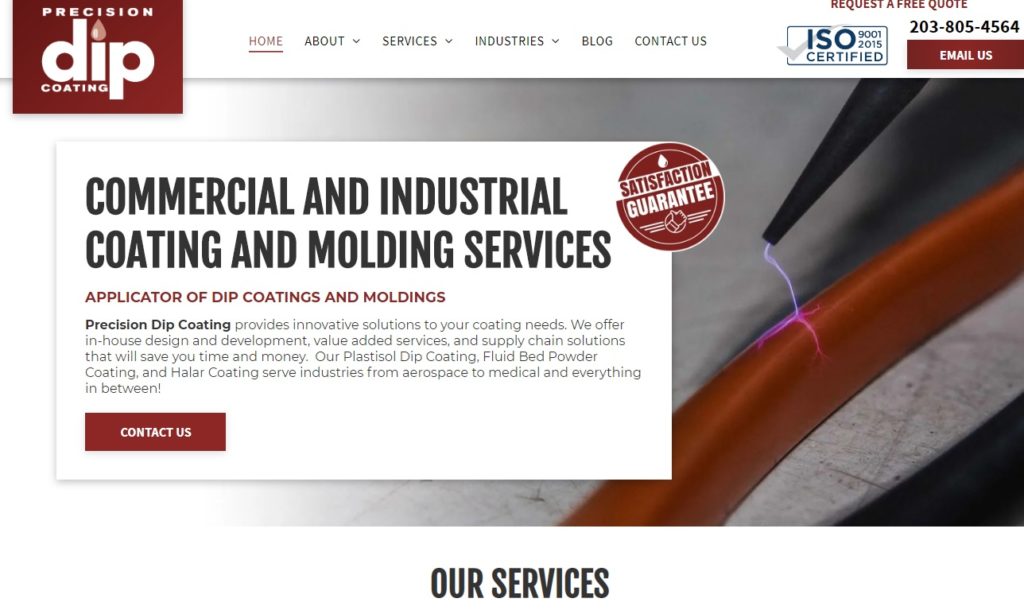
Carlisle Plastics is a dip molding plastics manufacturer offering end caps, plastisol paint masks, thread protectors, tube closures, protective caps and decorative caps.
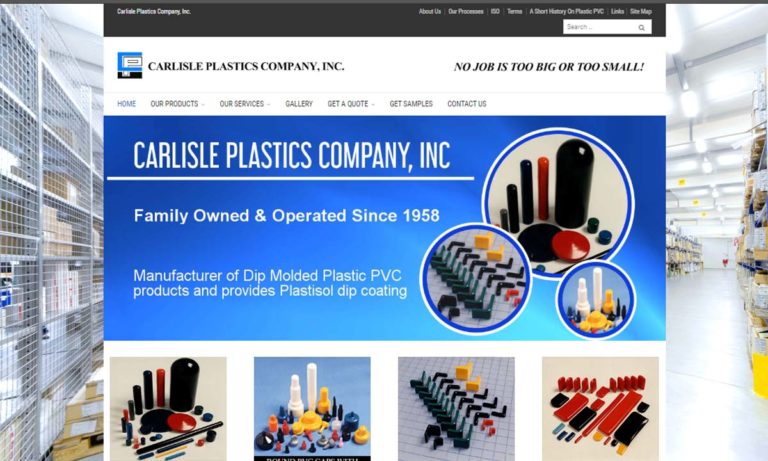
Rubber & Plastics Company has 50 years of experience in manufacturing dip molding with the materials, equipment and flexibility to rapidly prototype. We provide standard and custom designed high-temp paint masks, caps, grips and plugs.
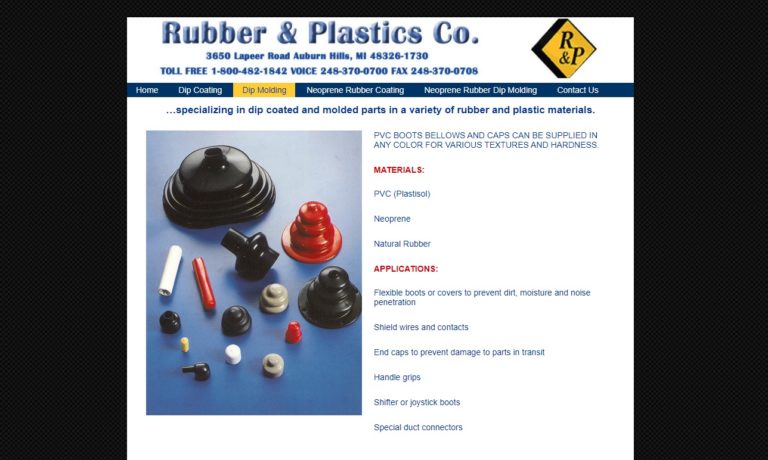
Innovative Coatings is a manufacturer of plastisol dip molding and fluidized bed powder coatings of epoxy, polyolefins, nylon and vinyl. Our dip coatings are of FDA-approved and biomedical grades.

More Plastic Coating Companies
Plastic Coating?
Plastic coating increases the tensile strength and service life of a metal object. It provides end users comfort and protection by offering gripping and insulating surfaces. Two more properties of plastic coating are electrical and thermal insulation. Many hand tools, including tongs and spatulas, also feature additional safety measures when handling hot things. In electrical components like wires, cables, digital meter probes, and so on, plastic coverings also act as insulation.

Types of Plastic Coating Polymers
The types of plastic coating polymers include:
Latex
Latex is made of a very thin emulsion of polymer particles (30-40 percent of which are rubber particles). It serves as the primary component of either natural or synthetic rubber manufacturing. This polymer is easily accessible and safe. However, some people experience allergic reactions once it breaks down into powder, which reduces its appeal.

Plastisol
Plastisol is the most typical polymer in dip molding and coating procedures. Fine polyvinyl chloride (PVC) resins are used to make it and are suspended in a liquid plasticizer. When heated, it solidifies into a soft, flexible, rubber-like substance and returns to its liquid state upon cooling.
The toughness, superior corrosion resistance, and impact resistance of plastisol coating are well known. It is ideal for electrical applications because of its high dielectric strength. Colorants are added to alter the final product's finish.
Epoxy
Once the polymeric chains have been cross-linked, epoxy is a thermosetting polymer that creates coatings with great strength, chemical resistance, and thermal resistance.
Polyurethane
A carbamate link connects the urethane (or ethyl carbamate) units that make up polyurethane. It is renowned for its adaptability and great deformation resistance.
Neoprene
Neoprene, a latex alternative, is made when chloroprene is polymerized. It is renowned for both its elasticity and resistance to chemicals.
Plastic Coating Process
Dip molding is the process of casting a plastic substance into an existing metal object. The coated metal serves as a mold for the plastic or polymer to adhere to during the process. Before being dropped into the liquid polymer, the component (or occasionally the entire piece) to be dipped or submerged is prepared and heated.
When the liquid polymer is cooled, it hardens and sticks to the metal. Except for the additional demolding or unloading stage, dip molding and dip coating are similar processes. Single, hollow, and double-walled items can be produced using dip molding.
Due to this, further downstream procedures like trimming and deflashing are no longer necessary. The approach conserves raw materials by using fewer subtractive secondary procedures.
Latex gloves, fashion and costume accessories, cups, plastic closures, and recreational equipment components are a few examples of dip-molded plastic products.

Advantages of Plastic Coating
- Heavy machinery and industrial equipment operate with natural vibrations as a side effect. Facilities put in a lot of effort to lessen and suppress vibrations to develop durable devices. Plastic coatings are a significant component of the effort because they reduce vibrations and stop machinery from making touch with one another.
- Despite several efforts to lower noise levels in manufacturing operations, noise is still a significant industry component because making many items requires a lot of force. Plastic coatings are used as separators, gaskets, shields, controls, and enclosures to reduce noise and vibration.
- The efficiency and smooth completion of various manufacturing procedures can be enhanced by reducing friction in an industrial process. Equipment can suffer wear, abrasions, and EMFs from friction, which can be harmful. Applying plastic coatings to various process components significantly decreases friction, enhancing productivity and safety.
- Modern industrial machinery is made with some insulation to safeguard workers and the items they produce. Due to their strength, simplicity of installation, and lifespan, plastic coatings are frequently employed. EMFs are lessened, metal-on-metal contact is avoided, and equipment runs smoothly thanks to a plastic coating.
Choosing the Right Plastic Coating Business
For the most beneficial outcome when selecting a plastic coating company, it is important to compare several companies using our directory of plastic coating businesses. Each plastic coating company has a business profile page highlighting their areas of experience and capabilities, along with a contact form to directly communicate with the business for more information or request a quote. Review each plastic dip coating company website using our patented website previewer to gain a better understanding of what each business specializes in. Then, use our simple RFQ form to contact multiple plastic coating companies with the same form.